2011 Chevrolet Cruze Crash Testing - Click above for high-res image gallery
Over the course of Bob Lutz' tenure at General Motors, one of his major goals was globalizing the production process. As Lutz tells it, the Pontiac GTO was the first global vehicle born of his labors, with development work being done in both Australia and North America. But the GTO, and its follow-up, the Pontiac G8/Holden Commodore, were niche products sold in limited numbers in limited markets. The real test of global product development comes when it's applied to high-volume mainstream products.
That's were the Epsilon II and Delta II architectures come into play. Epsilon is GM's mid-large platform (D/E segment) while Delta is the compact (C segment) platform. We've already seen the Epsilon II here in America, underpinning the Buick LaCrosse, but the Chevrolet Cruze proved to be a tougher nut to crack. One of the most difficult challenges in the global production strategy is the differing safety standards around the world, along with the guidelines imposed by non-governmental bodies like the Insurance Institute for Highway Safety (IIHS). Creating a platform that can live up to all of these standards without being absurdly heavy is a problem. Find out how GM tackled the problem and found a solution after the jump.
GM has been conducting vehicle crash tests at its Milford Proving Ground since the 1930s, and the current barrier test facility began its life in 1962. The main barrier consists of a 140,000 pound reinforced concrete block set into bed rock. Tens of thousands of vehicles have crashed into this block over its near five-decade existence, yet it's never sustained a crack and hasn't moved. An inch. When it was originally installed it was actually outdoors, but when the time came to upgrade, rather than build a new barrier, GM simply erected a building around it. The highest crash speed ever done at the facility was 78 miles per hour – nearly four times the energy of a 40 mph test.
In its current form there are four electric motors with a total of 2,400 horsepower that yank on a tow cable to accelerate a vehicle into the barrier. The safety engineers can conduct 52 different types of tests in the facility, including straight, offset, side- and rear-impact tests. As you'd suspect, performing a crash test is much more complex than simply slamming a car into a wall and calling it a day. Because of the all the different regulations that must be met, a vast array of instruments are installed in the vehicle, along with another host of instruments attached to the dummies.
%Video-1163%
Because crashes happen in just fractions of a second, it's critical to record everything that occurs. As many as 30-40 still and video cameras are used to record an event from various angles, including the interior of the car. The video cameras can record high-resolution video at up to 3,000 frames per second. According to Albert Ware, director of the vehicle safety crash-worthiness lab at Milford, approximately 11,000 videos and 72,000 still images are recorded. Every. Year.
Because of the high cost of vehicle crash testing, it's critical to ensure that valuable data is captured the first time a test is run. In the adjacent rollover test facility there's a 120-foot-long lighting rig hanging from the ceiling that can be lowered and adjusted in order to make sure everything is illuminated. Readers might notice that various parts of the car, including the wheels, engines and transmissions, may be painted different colors during crash testing. This is done to make it easier for the engineers analyzing the photos and video to see the relative motion of parts during a crash event.
The rollover test facility is among the newest safety facilities in the GM network. It was opened in 2006 and cost $10 million to construct and is the only such facility owned and operated by an automaker in North America. The engineers can conduct an array of different tests including a trip test to evaluate what happens when the vehicle slides sideways into a curb or other obstruction. A ramp is available to test what happens if the vehicle rides up over a guard-rail and other reconfigurable structures can evaluate the results of running off into a ditch.
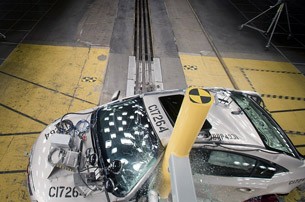
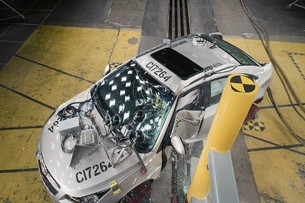
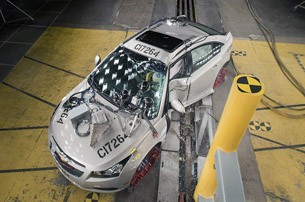
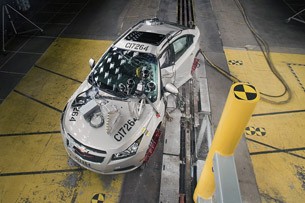
During our visit to the crash test facility we witnessed a side pole impact test where the car slid sideways at a 20 degree angle at 20 mph into a pole directly in line with the driver. The whole event lasted less than a tenth of second, but so much data was gathered that engineers will probably spend anywhere between two to four weeks analyzing it. In all, GM conducts about 300 vehicle crash tests a year at facilities in Michigan, Germany and South Korea, with about 160 of those at Milford.
In order to build vehicles that meet divergent crash requirements around the world it takes a lot more than just a few dozen tests per vehicle. Setting up a vehicle for a crash test can take several weeks and costs a lot of money. And it can only be repeated once and then the remains of the car are crushed after analysis, melted down and recycled.
In addition to full vehicle tests, GM makes extensive use of subsystem, component and simulation tests using three special sleds. A jig is set up with the passenger compartment of a new vehicle and the cabin is heavily reinforced to maintain its positional integrity during testing. Parts of the interior, including seats and dashboards, are installed in the test rig which is then mounted on the sled. Data from actual barrier crash tests is used to produce an acceleration profile of what happens to the driver and passengers in the vehicle.
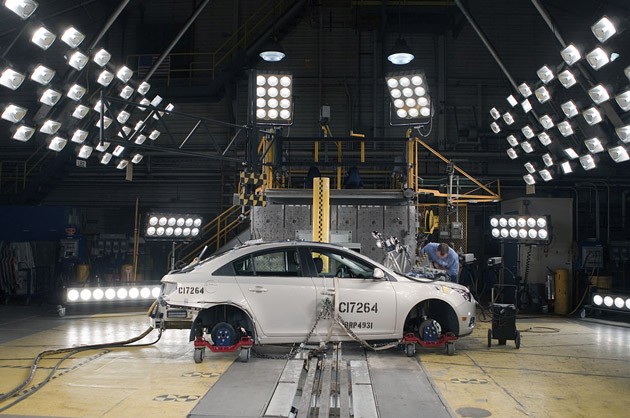
When the sled is activated, it replicates the forces seen during a crash event. The test sled mechanism has a frequency response of 150 Hz with a force of 2,500,000 newtons (562,000 pounds). It can adjust the rate of acceleration 150 times per second and can accelerate 40 times faster than a Corvette. We saw an air bag test conducted on one of three sleds at the proving ground and the acceleration tracked the input profile that was recorded on a previous barrier test very closely.
The advantage of these test sleds is that events can be run much more frequently and the only parts that need to be replaced are the air bag modules or seat belts. Tests can also be run with different sized crash test dummies to verify that no matter the shape or size of the passengers or drivers, they're all adequately protected.
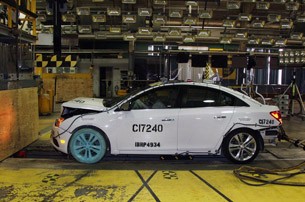
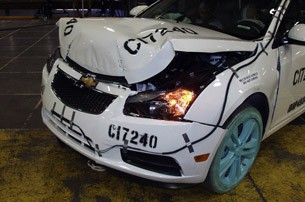
GM has over 200 crash test dummies of various sizes at the Milford test labs ranging from infants to 95th percentile males, and another 200 dummies populate GM safety labs around the world. The dummies cost between $100,000–$150,000 each and a typical unit has enough load sensors to measure the amount of pressure being exerted on all of its limbs, torso, head, neck and other parts subject to injury. The dummies are made from rubber, vinyl and steel, and are regularly subjected to known dynamic tests to verify the sensor signal accuracy.
The dummies are rarely discarded completely, and instead various parts will be replaced as needed and new dummies will be added as new types are developed. There are also specific tests that only use parts of dummies, including work in the "free motion" head lab. This lab verifies compliance with federal motor vehicle safety standard 201, which covers head impact with the vehicle's headliner. An instrumented head form is launched into various locations on the vehicle headliner with a nitrogen powered impacter (insert head-banging joke here).
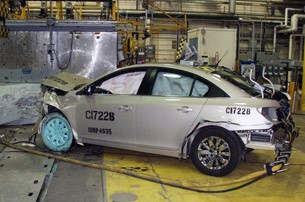
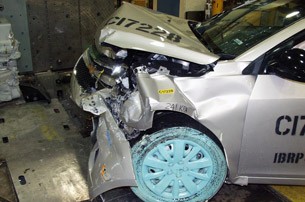
Even with all of this hardware testing, it still wouldn't be practical to develop a single design that meets global safety standards without some help. Long before the first pieces of steel are cut, stamped and welded, the engineers have done thousands of crash tests on computers. Mathematical models of the body structures have become increasingly sophisticated over the past 30 years. Every time a real body or airbag is tested, the results are compared against the simulation of the same test to tweak the model and improve its accuracy for future development.
More accurate models allow the engineers to evaluate potential crash scenarios and optimize the structure without adding excess mass. GM hasn't released officials weights yet for the Cruze, but we expect it to be somewhere between 3,100 and 3,300 pounds. We were shown a Cruze that had been through a 40 mph offset barrier crash test and the main passenger compartment area was completely intact. The doors opened and closed with almost no more resistance than on a new vehicle.
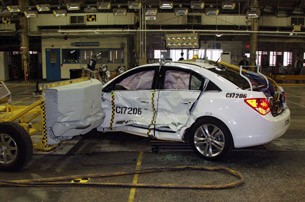

Approximately 64 percent of the Cruze body is made from high strength steels. The structure also makes use of tailor rolled steel for stampings on the B-pillar. Tailor rolled steel blanks are made from sheets of various thickness to provide additional strength where needed while eliminating weight where it isn't necessary. The Cruze is the first car in its class with 10 standard air bags, including knee air bags for both front seat occupants, side curtain air bags and seat back mounted side airbags at all four outboard positions. The Cruze has also received five-star crash safety ratings in Korean, Chinese, Australian and European NCAP tests. On the EuroNCAP, the Cruze got the highest score ever recorded for a compact vehicle, and GM fully expects to get the highest rating in the U.S. as well.
In addition to the protection provided by the body and all of the air bags, the Cruze also has standard electronic stability control to help prevent crashes from happening in the first place. After a crash the OnStar system automatically notifies emergency responders to provide assistance. Thanks to the crash-worthiness technology developed by General Motors over the past several decades, the Cruze could be one of the safest vehicles ever built. And the lessons that its team learns today will be applied to vehicles for years to come.
Sign in to post
Please sign in to leave a comment.
Continue