Click above to view more high-res shots of the R8 under construction
This week Audi invited a group of American journalists to Europe to sample the newest A4 Avant, and since we hate to miss an opportunity to drive new cars, we hopped on a plane. Upon our arrival, Audi offered us the chance to visit the birthplace of the mighty R8 in Neckarsulm, which is home to one Audi's two main German manufacturing sites, the other being at its headquarters in Ingolstadt. The Neckarsulm complex is only about half the size of the Ingolstadt campus, but along with manufacturing the A4, A6 and A8, it is also home to Quattro GmbH.
Quattro GmbH is Audi's in-house tuning group, roughly equivalent to AMG at Mercedes-Benz and the M-Division at BMW. That means all S and RS models are developed here and the RS4 and RS6 are built here in addition to the R8. The R8 is built in a dedicated building by a team of 240 specially selected assemblers working on two shifts. Right now, the R8 team is turning out about 27 to 28 cars per day, but Audi's manufacturing engineers are refining the process to try up that to 30 cars per day. Read on to learn more about how and where the R8 is created.
This week Audi invited a group of American journalists to Europe to sample the newest A4 Avant, and since we hate to miss an opportunity to drive new cars, we hopped on a plane. Upon our arrival, Audi offered us the chance to visit the birthplace of the mighty R8 in Neckarsulm, which is home to one Audi's two main German manufacturing sites, the other being at its headquarters in Ingolstadt. The Neckarsulm complex is only about half the size of the Ingolstadt campus, but along with manufacturing the A4, A6 and A8, it is also home to Quattro GmbH.
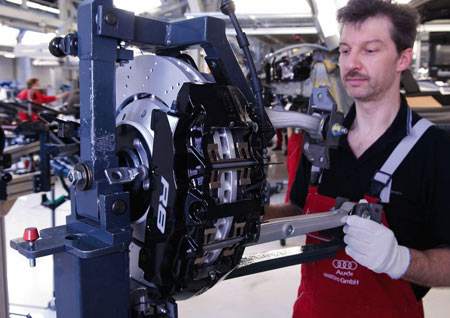
Like the Lamborghini Gallardo with which it shares some technology, the R8 is built using the Audi Space Frame design that was pioneered on the original A8 and later the A2. The main structure of the car and the body is made almost entirely of aluminum. R8 production takes place in two main halls within the dedicated building at Neckarsulm, and the process starts in the body shop before moving into the final assembly hall. In the body shop, the supporting structure is assembled largely by hand from a series of aluminum extrusions. Unlike a typical high volume body shop were all the pieces are assembled and welded by robots, all the welding on the R8 is done by humans.
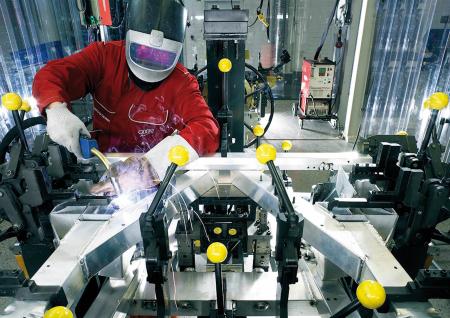
At each of several stations, the assemblers take a handful of components that make up one of several sub-assemblies and clamp them into a jig that precisely locates the parts relative to each other. Then they put on their masks, grab their welders and start the process of fusing the extrusions together (see above). Once the smaller sub-assemblies are complete, they go into a larger jig to be located relative to each other again. In this station, one of the six robots that are used in the plant apply rivets to hold the pieces together until the welders go at it again.
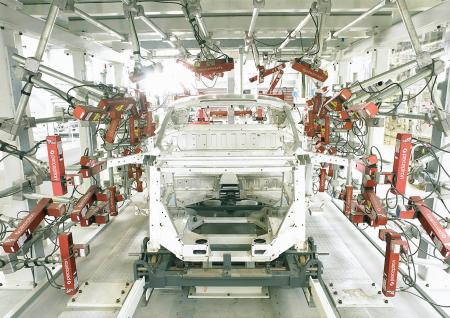
Some components such as the floor pan are joined to the space frame with screws so that they can be replaced if necessary. For this, another pair of robots are used that drive in special self tapping screws. The aluminum around the screws softens as the screws are driven in and the material forms a thread around the screw. The one bit of robot welding in the entire process is to attach the bolts to which the suspension components are mounted. After the remainder of the aluminum body is attached, the whole thing goes through a booth where several dozen lasers scan the body for dimensional errors (see above). After that, the body is milled or welded as needed before heading off to the paint shop. Each body stays in the paint shop for four days being coated and cured before moving on to the final assembly hall.
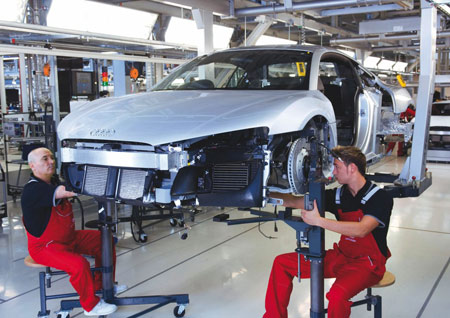
In the final assembly hall, all the various sundry components that make up a car get added. The assembly line here, though, is a semi-moving affair. The cars sit stationary at each station for 32 minutes while a team of assemblers installs whatever goes on at that point (see above). Audi engineers are currently working to reduce each station time to 30 minutes in order to meet that 30 car per day production target. At each station, one member of the team goes off to the racks around the outside of the line with a shopping list based on that vehicle's particular build sheet and collects the necessary parts for that car.
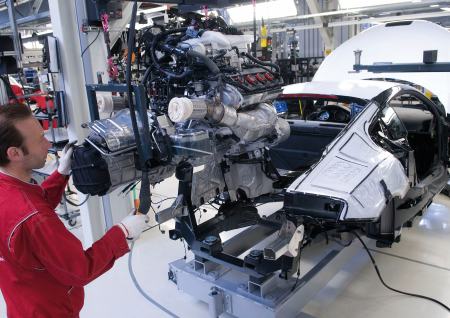
Along the way, wiring harnesses, instrument clusters and the twin fuel tanks are added. The 4.2L V8 engines are delivered daily from Audi's engine plant in Gyor, Hungary. The Gyor plant builds all the engines for every Audi model, while both manual and automatic transmissions for the R8 are produced at Lamborghini's facility in Sant A'gata, Italy. A close look at the transmission casing of the R8 reveals that it has both the Audi four ring logo and the Lamborghini raging bull logo cast on it. The engines and transmissions are assembled along with the wiring harness on a sub-assembly line before the whole powertrain is slid into the car from the back (see above).
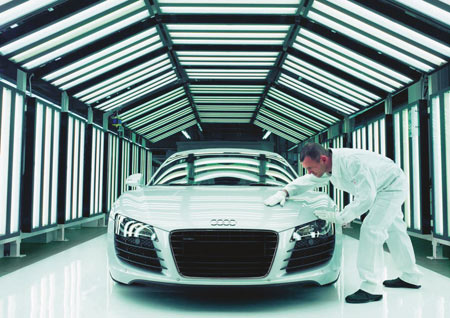
At the end of the assembly process, after the wheels have been put on and the car is lowered to the floor for the first time, it gets fired up before being driven over to the staging area for the rolls test. All car factories have an end-of-line rolls tester where the car is driven up to a moderate speed so that systems like lights, steering, transmissions and brakes can be checked out. On the R8 rolls tester, the cars are run up to 180km/h (112mph) before they are allowed out of the factory. Once a car passes the rolls test, it is taken out to the test track to be driven with some of the cars also getting an open road test.
In total it takes about 7 - 8 days to produce an Audi R8 from the time the first parts are collected until it is driven out the door. Last year, the Neckarsulm factory produced 4,125 R8 models and has plans for almost 5,500 in 2008. Obviously the company doesn't like to talk about future variations, but no doubt there will be some. Whether those include a V12 TDI (more likely a 4.2 TDI) or twin-turbo V10 is anyone's guess right now. The only thing that is known is that they will roll out of this same dedicated factory after being welded, screwed, glued and snapped together by Audi's best workers.
Sign in to post
Please sign in to leave a comment.
Continue