HRE Open House 2011 – Click above for high-res image gallery
If you asked a group of enthusiasts what company makes the best wheels, the answers would undoubtedly be varied. HRE, however, would probably be mentioned in that conversation. The HRE Peformance Wheels team has been creating rollers for everything from luxury cruisers to some of the most exciting vehicles in motorsports.
The current lineup of HRE wheels is as impressive as it is expensive. Wheels start at around $1,300 per corner. Curious to learn how the company justifies charging so much for its wares, we traveled to the company's Vista, California headquarters for its recent 2011 HRE Open House. We wound up with an inside view at how the wheels are made and a peek at the company's diverse (and loyal) customer base.
The HRE Open House is an annual event that lets fans of the company check out how their favorite wheels are produced. The open-door get-together is also a chance for people to hang out and check out a wide range of vehicles. Four-wheeled attendees ranges from a Koenigsegg CCX and Ariel Atom, to a Mercedes-Benz 300SL and Chris Rado's wild Time Attack Scion tC.
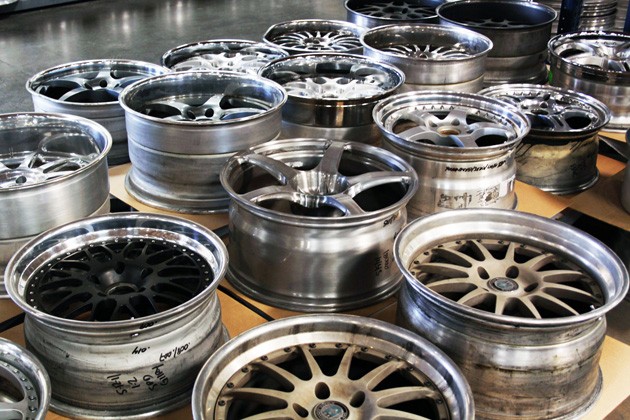
We'd get a chance to look at the cars in a bit, but we mostly wanted to learn more about the wheels they were wearing. The President of HRE, Alan Peltier was on hand to give tours through his facility and provide insight into how the product moves from a computer design into a finished wheel.
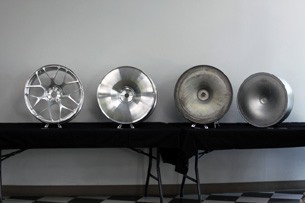
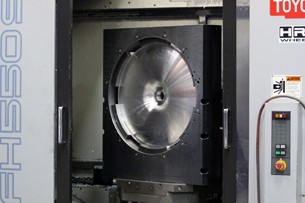
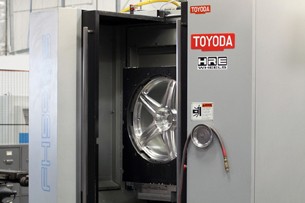
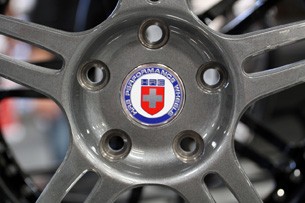
HRE builds two types of wheels; three-piece forged (or spun) wheels and its well-known Monoblok one-piece forged unit (think: HRE P40). All wheels begin life in the head of either a designer or an engineer. From there, the potential design is entered into a computer modeling system called Finite Element Analysis, which allows the HRE team to model how physics will affect their wheel. The FEA program shows an engineer how a given design will respond to the effects of speed, weight and a variety of g-forces. After the wheel gets a green light, it's time to begin the physical process of manufacturing.
The average aluminum wheel found on stock vehicle is created by pouring a molten alloy into a mold. HRE takes a different approach. The three-piece wheels begin with an outer barrel, which starts out as a flat disk of high-strength aluminum that is worked into shape in a manner similar to a potter spinning clay. The barrel is turned into two halves, which allows HRE to build wheels to custom requested widths. The third part of the three-piece wheel starts out as a chunk of aerospace-grade aluminum which gets forced into a disk shape. That disk is then sent to the CNC machine so that the spoke pattern can be created. Put the two halves and center portion together, and voilà! You have an HRE three-piece wheel.
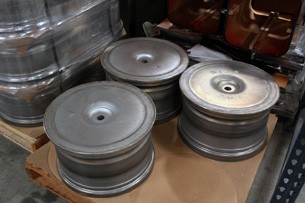
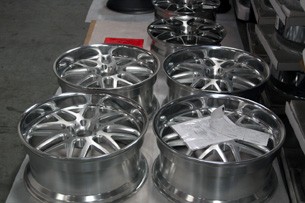
If you're looking for something stronger than the already burly three-piece, HRE might direct you to its one-piece Monoblok. This wheel starts out life as a solid block of aluminum. The metal is forged, thanks to a combination of heat and pressure, into a round shape. That wheel-like chunk of aluminum is loaded into a form-flowing machine to create a barrel, and then into a variety of CNC machines to create the lock initially dreamed up by HRE's designers.
Both the three-piece and Monoblok one-piece aren't done when they pop out of the CNC machine. The wheels are inspected, deburred and then polished by hand. The entire finishing process can take up to eight hours per wheel, and all are certified to meet Germany's strict TÜV standards. It's this sort of attention to detail that helps HRE command premium pricing in the wheel market.
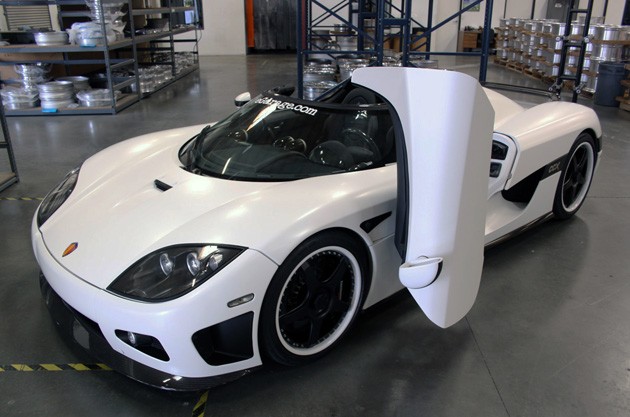
HRE's open house was attended by a range of enthusiasts, as well as a plethora of high-performance machines. eGarage was on hand with a Koenigsegg CCX, Ariel Atom, Bentley Continental Supersports and an sinister old Chevrolet Camaro hiding 2000 horsepower under its hood. Tanner Foust showed up in his BBI-tuned Porsche. HRE fans also drove into the parking lot piloting brands like Ferrari, Lamborghini, Audi, BMW and Porsche, not to mention a few clean examples of the Acura NSX, a Datsun 240Z, some Ford Mustang models, a handful of Volkswagen offerings and even an Alfa Romeo GTV.
Not everyone can – or would choose – to spend the type of coin that HRE asks for its wares, but events like the company's open house are very smart, if for no other reason that they give prospective customers a first-hand look at what makes their products so special.
Sign in to post
Please sign in to leave a comment.
Continue