Autoblog tours Pratt & Miller shop – Click above for high-res image gallery
Racing improves the breed. How many times have you heard some automaker PR flack spout that line in order to justify a motorsports program? When it comes to NASCAR, which is still the most popular form of racing in the United States, it's clearly a complete fallacy. Open wheel racing, be it at Indianapolis or Monaco, largely falls into the same bucket. There is, however, one form of motorsports where there truly is a feedback loop: sports car racing like the kind on display in the American Le Mans Series.
One example is staring you in the face every time you look at the nose of a contemporary Corvette. When the C6 Corvette debuted, many fans complained about the styling, including the front air intake and the departure of the long running pop-up headlamps. The C6 brought a new larger central air intake and exposed, flush lighting. The design was influenced directly by the C5.R racing program and its need for better air-flow to the engine and brakes of the racecar. Learn more about the connection between Corvette production and racing after the jump.
With the opening race of the 2010 American Le Mans Series campaign just a couple of weeks away, the Corvette Racing team invited us out to the Pratt & Miller shop in Wixom, MI to learn more about their program and the race car. Corvette Racing is one of only two major racing program sponsorships that survived the General Motors bankruptcy with NASCAR being the other. In the case of NASCAR, relevance to product or improving the breed clearly doesn't factor into the equation. NASCAR is about marketing plain and simple, and how effective it is for that is debatable.
Ever since the Corvette Racing program had its competition debut at the 1999 24 Hours of Daytona, Pratt & Miller Engineering has been part of the program. When the program began, former Corvette chief engineer Dave Hill decreed that the effort must have a close relationship with the production engineering team to ensure that there was technology transfer that benefited road and race cars alike. That transfer began early and has continued.
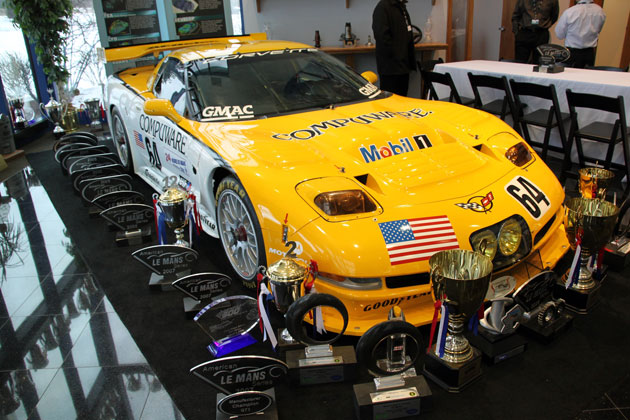
The 1999 racecar was based on the then-current C5 Corvette, and since GT cars are required to retain certain dimensional commonality with production models, the shape of the fascia caused problems. The two slim horizontal inlets on the nose of the C5 and the small central under-bumper intake made cooling the engine and brakes a real challenge. When the time came to develop the C6, knowing that a racecar was to be part of the plan, the production team opted for a single large central air intake to feed both the brakes and engine. The result was much improved air-flow performance for both versions.
Pratt & Miller has two other facilities in North Carolina in addition to the Wixom shop. One supports General Motors' NASCAR programs while the other works primarily on military programs. Wixom focuses on road racing efforts, which are currently centered around Corvette and some Grand Am customer support programs. Walking into the lobby of the 100,000 square foot Wixom building, one is immediately reminded that this is a serious racing operation with a long and very successful competition history. The walls of the lobby are lined with dozens of race and championship trophies. The standards are very high here.
The Corvette C6.R initially begins coming to life in the P&M engineering office, which is filled with Unigraphics computer aided design workstations. The race engineers are using exactly the same software as the production engineers 30 miles east in Warren. The race facility also has a direct data connection to Warren and the team works from the production computer vehicle models as they develop the custom competition parts. Data is continuously flowing back and forth between the two teams.
Some of Pratt & Miller's simulation capabilities and expertise even go beyond what General Motors has at its disposal. For example, Corvette Racing communications manager Doug Fehan tells Autoblog that no wind tunnel testing has ever been done on the C6.R. The team relies entirely on computational fluid dynamics (CFD) models to do its aerodynamic development. Over the last decade, the models have been developed, calibrated and validated by instrumenting the car and running at racetracks as well as a two-mile-long runway to ensure that real results equal predicted results. The end result is reduced costs by not having to build tunnel models and then book time to test them.
The engineers can go through far more aerodynamic iterations on the computer than they can in the tunnel and the success that Corvettes have had on the track seem to demonstrate the value of this process. P&M's CFD capabilities are such that when Corvette chief engineer Tadge Juechter's team ran into a problem during development of the ZR1, they went to the race team for help.
The ZR1 uses massive carbon ceramic brakes by Brembo (below, right). While the brakes can turn huge quantities of kinetic energy into thermal energy in a very short span of time, that heat needs to be dissipated, which requires air flowing over the rotors. In spite of plenty of duct work from the front air inlet, the engineers couldn't get the brake temperatures down.
The P&M engineers pulled the ZR1 model into their CFD system and quickly determined that at high speeds there was so much turbulence around the wheels that the air from the ducts was literally getting sucked right out around the outer edge of the wheel and into the wheel well, never coming anywhere near the rotor. Over the course of a couple of weeks, they designed and fabricated a system of ducts and baffles to control the air-flow around the ZR1 wheels and allow the cooling air to do its job on the brakes. Racing improves the breed again.
Once the engineers create their computer models, they can produce initial plastic 3D models on a stereo lithography machine right in the office. They then take those plastic parts out to the shop and verify that everything fits properly on the car before sending the computer models to the CNC programmer for fabrication. P&M has six computerized numerical control (CNC) machines in the shop that are used to fabricate parts like mounting brackets, control arms, pedal boxes, etc.
P&M builds almost all parts of the racecar in-house in order to ensure quality and reliability, something that is paramount in endurance racing. Every part that comes through P&M is either laser etched with a serial number or bar-coded and cataloged. Every part is also checked with laser measuring equipment supplied by Faro. Faro builds laser measuring equipment and is located just down the street from P&M. The two companies work closely together and Faro uses P&M to help test its latest equipment. With all of the parts cataloged, the team has a complete record of its entire history and can go back find the root cause of a fault in the rare instance when something fails on the track.
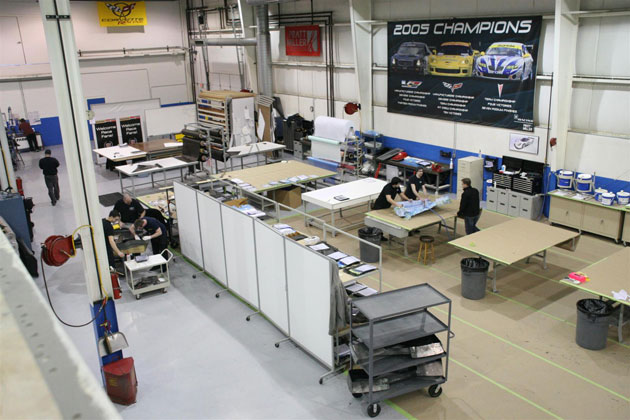
Adjacent to the machining area are four large surface plates where chassis are assembled. The surface plates are used to ensure that the geometry of the chassis is as consistent as possible so that new parts will work properly and settings can be transferred to another car if something changes. A fourth GT2 C6.R chassis was coming together on one plate while we were in the shop. On an adjacent plate, the crew was doing a conversion of a Pontiac G6 GXP to a Camaro. The G6 was built on rear-drive tube frame chassis by Pratt & Miller and the company has developed a conversion kit to turn it into a Camaro. Fortunately, the dimensions of the GXP work perfectly for the new body and the first conversion ran at the opening round at Daytona.
Technicians were also building wiring harnesses for the racecars in one area of the shop, another job that is done in-house to ensure quality and durability. Next to the electrical shop was the composites area (above). You guessed it, Pratt & Miller does all of its own composites work from cutting up sheets of carbon and kevlar from huge spools of woven material to lay up and even making the molds. A giant autoclave sits in a corner of the shop and the cycle time to produce each part is about 24 hours from start to finish. The Wixom shop also produces composite parts for the military operations facility in North Carolina, which is why we were not allowed to take any photography inside the shop.
The C6.R switched classes in the American Le Mans Series in mid-2009 from GT1 to GT2. The GT2 class cars are even more restricted than the GT1 class and aside from the fenders (limited to 2 meters in width), the engine air vent in the hood and the front air opening, the rest of the car is dimensionally identical to the road car, which includes the rear lip spoiler on the ZR1. The engineers found that the little spoiler actually works very well with the GT2 spec wing and rear diffuser to aid down-force.
The last section of the shop we visited is the final build area. The last example of the GT1 cars was sitting in the far bay waiting for someone to step up and buy it (contact Pratt & Miller if you need a GT1 C6.R ready to race). GT2 chassis #1 was also on display and ready to be packed up for shipment to Sebring next week for the season opener, the 12 Hours of Sebring. Chassis 2 and 3 were in various stages of assembly.
Chassis #1 was the car that Jan Magnussen had his huge crash in at the season ender in Laguna Seca last fall. To provide a clue about how tough these cars are, Magnussen walked away from the spectacular incident with only bruises. The car was launched into the air and then landed on the track nose first at 45 miles per hour. The impact deceleration was measured at 57 g. All of the damage was confined to the front of the chassis structure and according to Juechter the acceleration remained almost flat throughout the event. This is important because it indicates that the structure is absorbing the energy of the impact at a steady rate without any huge impulses. Those energy spikes are what often cause more severe injuries.
When the car was returned to Wixom a few days after the race, it was stripped down and the chassis was placed on the surface plate. Everything from the A-pillars back was intact and within tolerances. Only the structure ahead of the front axle center line was damaged. The crew cut off the structure ahead of the firewall and welded on a new one. Two weeks later chassis #1 was back on the track being tested.
A surprising number of parts on the GT2 car are production components including the full windshield frame, the steering system including the tilt/telescope steering column and the primary chassis structure. When the GT1 car was developed, the team opted to use the steel chassis of the base Corvette as the starting point to ensure they didn't have issues with attaching a steel roll cage to an aluminum structure. Joining dissimilar materials is problematic because it can trigger galvanic corrosion and weakening of the joints. Companies like Ferrari and Porsche use a large clamp around aluminum structures to attach their roll cages.
Corvette Racing wanted something tougher and at the same time more elegant. They developed a tapered aluminum sleeve that threads into the aluminum rocker panel beam. That sleeve is then welded to the beam. A steel stud is inserted into the sleeve with a special adhesive filled with 0.020 inch diameter silica micro-spheres. As the stud is tightened, the adhesive keeps it in place while the glass micro-spheres prevent any aluminum on steel contact. So far the process has worked great and the team has not found any evidence of fatigue cracks on the first two race chassis.
The biggest change to the cars for 2010 is a new 5.5-liter V8 engine replacing the 6.0-liter used last year. The 6.0-liter was a downsized version of the 7.0-liter GT1 engine that was built around a racing block and originally developed by Katech. The new 5.5-liter engine was developed in-house by GM Powertrain and is based on the production LS7 block from the Z06. The bore and stroke of the LS7 have been reduced to bring the displacement down and the aluminum heads are straight out of the GM performance parts catalog. The new engine was developed over the last couple of years when it appeared that new GT engine rules would come into effect for 2010 that limited displacement to 5.5 liters.
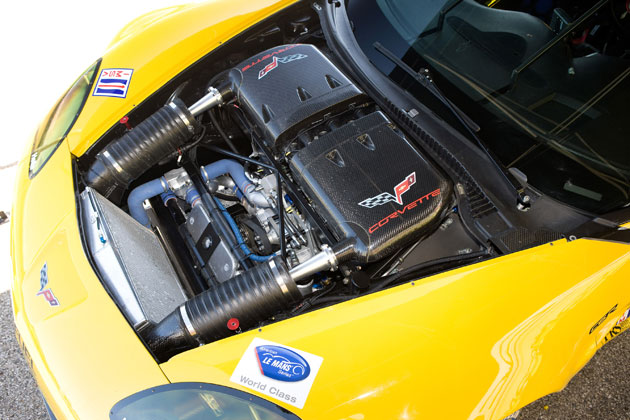
Those rules have been put back to at least 2011, but GM is racing the new engine because its small size allows slightly larger air restrictors (up to 28.8 millimeters from 28.6 millimeters for the 6.0). P&M Technical director Doug Louth wouldn't talk about specifics about power, although the press release lists 485 horsepower. The larger restrictors have allowed a slightly higher red-line for the smaller engine, which gives the team more flexibility with gearing for different tracks. The 5.5-liter engines are being built at GM's nearby Performance Build Center where all the dry-sump Corvette engines are assembled.
While most people don't think in terms of fuel efficiency when they consider racing, the engineers do, especially in endurance racing. Speed on the track is of paramount importance, but that only counts when the car is actually on the track. At a track as long as Le Mans at 8.5 miles, the number of laps between fuel stops is critical. During the Corvette's debut season, the cars were getting 10 laps per tank of fuel. Steady development of the car and powertrain meant that by 2009, they were getting 15 laps per tank while running faster than ever. Over the course of a 24-hour race, that many fewer fuel stops amounts to running anadditional 1.5 laps. With the lead cars now regularly running as close as 5–10 seconds apart at the end of 24 hours, those five minutes that are picked up in reduced fuel stops can easily make up the difference between victory and missing the podium altogether.
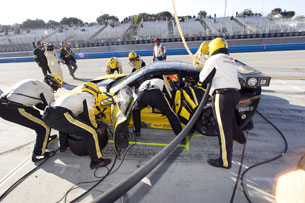
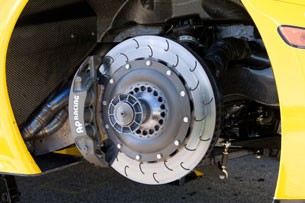
At a race like Le Mans or Sebring, the wheels of the racecar have to come off and go back on frequently. Anyone who has watched more than a few races has seen a pit crew struggle with a lug nut that was stripped or seen a wheel that separated from a car rolling down the track. One of the best examples of attention to detail at P&M is a custom lug nut and corresponding stud that is almost impossible to strip. The P&M engineers developed their own unique thread profile that is highly resistant to stripping and they machine wheel studs and nuts around this thread. The result is that they can get the wheels off and back on faster with less risk of jamming things up, which saves precious seconds in the pits.
Over the past decade, P&M built 20 1/2 GT1 Corvettes including the C5.R and C6.R. The half car was a development mule used to test some C6 parts on what was essentially a C5. Most of those cars have been sold off to other race teams and collectors and GT2 cars are now available to interested parties. Unfortunately, none of the GT2 cars have been ordered yet because of the tough economic times right now. Pratt & Miller charges $750,000 for a complete turn-key, ready-to-race GT2 C6.R, which Fehan explained is about 15 percent more than a Ferrari or Porsche. However, Fehan and Gary Pratt explained that the higher up-front cost comes with substantially lower operating costs and includes a full package of spares, instrumentation and support.
The V8 is rated for 40 hours of run-time between rebuilds, which is more than its competitors and the rebuild costs are substantially less. They cited the example of Aston Martin that requires signing up for a $250,000 engine support engineer before you can even fire up the engine. The robustness of the Corvettes has meant that many of the GT1 cars have been reliably running and winning in European GT competition for 3–4 years of more.
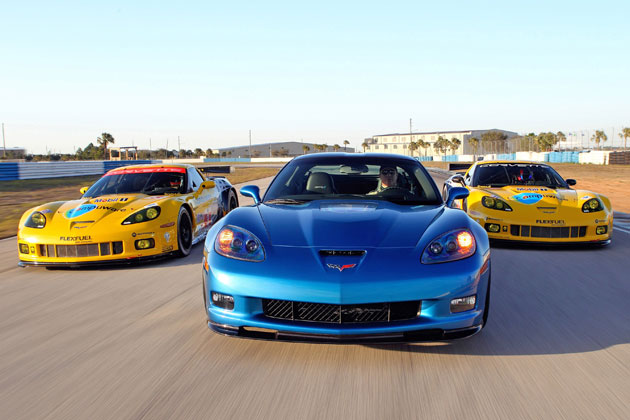
While the Corvette may be a comparatively cost effective race car, the obvious question is whether such a program makes financial sense for General Motors being so soon out of bankruptcy. None of the principals including Juechter, Fehan, Pratt or Louth would discuss specific spending numbers but they all emphasize that the program is very cost effective and has an excellent return on investment. They all said that during the bankruptcy process, government and financial types looked over every program and decided that this was one worth keeping around. We've previously heard from people like ALMS CEO Scott Atherton that the biggest budgets in the series for the top prototype teams were on the order of $40 million. A GT program like the Corvette is substantially less than that. Considering the technical and marketing benefits that the program has reportedly brought to the Corvette production program, that seems pretty cheap.
Fehan credits the long-term stability of Corvette Racing and the Pratt & Miller crew as one of the prime factors that has helped the team achieve such success. Many of the technicians and crew have been with Pratt & Miller since before the Corvette program began and most of the drivers have been along for several years. As a result they know each others' strengths and how best to get things done. Anyone new who walks in the front door sees all those trophies and immediately understands the standards that will be expected of them. That's the kind of professionalism that has made the likes of Penske, Ferrari and McLaren long-term successes and it continues to serve P&M and Corvette Racing well.
Sign in to post
Please sign in to leave a comment.
Continue